How to Order
Awarding You Offers These Ordering Options:
- On-line: we have hundreds of options available in our online store. You can search by material, shape, price range, color and more. Place your items in the shopping cart, add your text, billing and shipping information and hit Submit. You'll get a follow-up email with instructions on submitting your logo(s) to us for your order.
- Phone: 800-753-3384. Dial the extension for Sales and this will connect you with our Awards Consultants who can assist you with your order. See the list below that outlines the information you'll need to have ready to place your order.
- Email: you can email your order information to our sales and customer service teams at sales@awardingyou.com. See the list below for the information we’ll need to process your order.
Rush Orders: We have many options to help you successfully meet your deadline when the timeline is short, from one-week turnaround to overnight in some cases. These orders will incur a Rush Fee, ranging from 10% to 50%, depending on the product requested and the timeframe in which they are needed. Contact the sales@awardingyou.com team for more information.
- Order Confirmation:
You will be emailed an Order Confirmation from the Awards Consultant responsible for your order. If there is any additional information we require or if we have questions about your order, we will contact you to confirm these items. - Art Proof:
You will receive an Art Proof that lays your logo and text out on a template of the award and gift items. To see what an Art Proof looks like, view this Sample Art Proof. The timing of this is generally within several days of your order placement. The Art Proofs give you a chance to confirm spelling, grammar, etc. Please try to review these promptly to keep your order on schedule. See our Product Design Guide Below
If you know what products you want but won't have your text and recipient information available until closer to your event date, we encourage you to place your order now, so we can order materials and schedule your production order. You’ll need to have your text and logo to us approximately 5-10 days before your event.
- Production Time:
Standard production time for most Awarding You products is 10 days. Shipping time is 1-4 days depending on your location in North America. International shipping options (depending on the country & service chosen) can get your order to its destination within 5 business days. The production time for each product is specified on each product page, on the section labeled Packaging/Shipping. See our complete Packaging and Shipping Guide.
Please provide the actual date the awards are to be presented as well as the date you need them in hand.
- Shipment Tracking Documentation:
Once your order ships, you will receive an email with tracking documentation so you can check on the arrival date and time of your order.
Product Design, Artwork & Engraving Guide
Font and Logo Artwork
- Engraving text and logo?
We have a team of graphic artists that will take your logo and text and creatively lay them out on your chosen awards. Please indicate what text you would like on each item.
- If there is common text (to be engraved on a group of awards), please indicate that, and then if there is any unique text for the items.
- For orders with over 25 items, supplying the text in an Excel spreadsheet is recommended. Contact an Awards Consultant if you have any questions.
-
Font Choices
Here are the most common fonts that we recommend because they are easy to scale to size on different sizes of awards and gifts.
Basic Colors and Pantone Matching - Many customers choose to fill their engravings with color. Please have your color choices selected. Here is information on color choices for engrave fill:
- Basic colors: We have a variety of standard colors that can be used for paint filling. If you want your text in red, and your logo in a royal blue, we will be able to do this without Pantone Matching. In general, color fill adds between $15-30 per part.
- Pantone match: we cannot match Pantone colors exactly. However, we can come very close. This has been generally acceptable to all clients. There is a one-time fee of $50 per Pantone color matching.
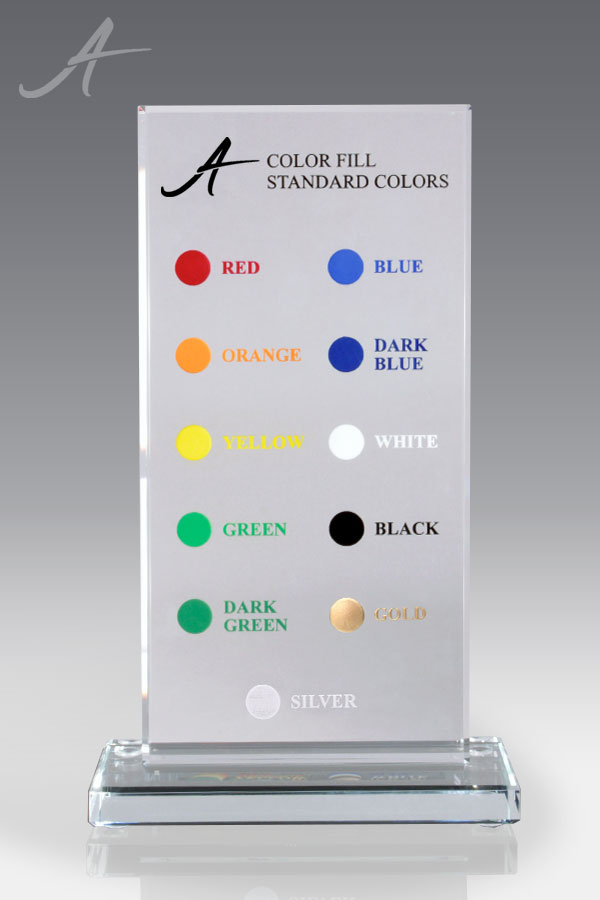
- Silver fill is an option for engraved text and logos on glass and crystal awards. It's used more frequently when there is a lot of copy on each award. This is a personal preference for customers who wish the copy to "pop" a bit more. The cost to add silver fill is $7.00 per award.
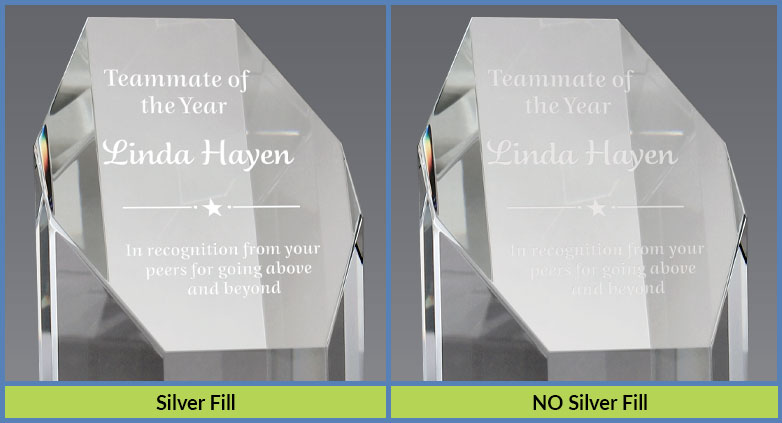
- Logo files are to be vector art images created by graphic programs such as Adobe Illustrator.
- The images need to be black line, no color or shading.
- The files need to be sent as .EPS or .AI format.
- Files that are not sent in this format may require additional time and cost for our graphic artists to redraw (costs range from $50-$150).
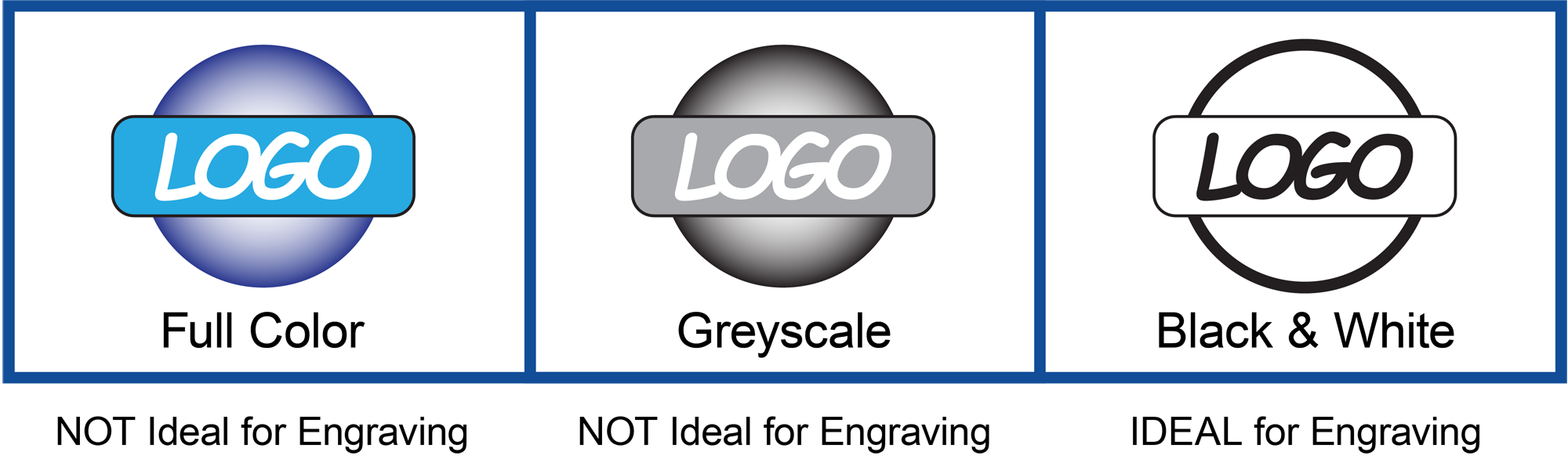
- Logo files are to be vector art images created by graphic programs such as Adobe Illustrator.
- The files need to be sent as .EPS format.
- Files that are not sent in this format may require additional time and cost for our graphic artists to redraw (costs range from $50-$150).
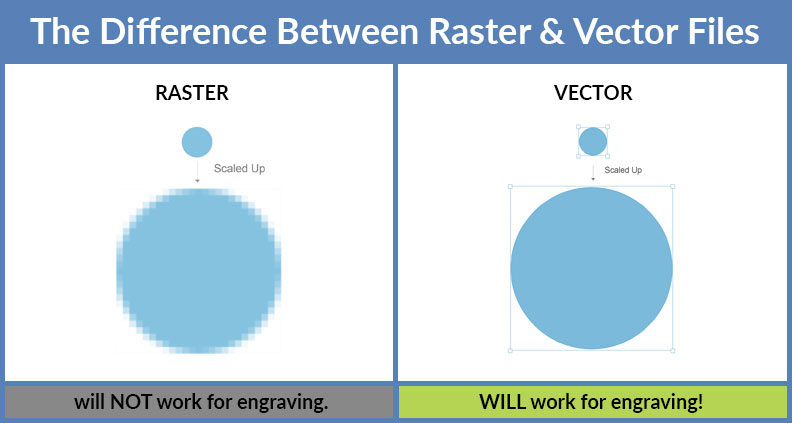
Need ideas? See our Award Ideas and Wording Guides
Artwork and Engraving FAQ
- What is an .EPS file?
EPS stands for Encapsulated Postscript. It is a file type that allows graphic images to be transferred from one format to another. EPS is a vector graphics format that we need for engraving logos into glass, crystal, and wood.
- What file type do you need for 3D images?
To sub-surface engrave a three-dimensional object on the inside of an award we use .MAX, .OBJ, .IGS, .STL, .DAE, .FBX, .SKP, .DWG, or .STP files.
- What is vector artwork?
Vector graphics are different than Raster graphics. Raster graphic files (JPEG, TIFF, Etc) are made up of pixels. These are great for printing and photo requirements. However, for engraving we need to Vector Art so that we can scale the logo to the engraving space on your award or gift item. More information on can be found on our Logo File Requirements section of our How to Order page.
- When can I get a proof?
Proofs are completed and a link for approval is sent to you typically within 2 to 4 business days of your order information being received (there are some exceptions to this - for long term orders, or when you don't have all your recipient information, we will wait to create proofs until closer to your shipping time).
Once your order is entered into our production system, the components for your product are scheduled for manufacturing. During that time, your text and logo are sent to our Art Department where our graphic artists will lay your materials out on a template of the award or gift item(s) on your order. They will create an online proof using our ProofStuff software and a link will be sent to you via email for your review and approval. This gives you the opportunity to double check all spelling, information, etc on your order before it is engraved.
- Can I get a proof before I order?
Generally, this is not how our process works. Proofs are completed within 2 to 4 business days after an order has been placed (depending on order size, type, etc.) at which time a link will be sent to you for reviewing and approving before production begins.
- What size font can you engrave?
In general, the smallest font we'd recommend is 10 point. However, this depends on the font chosen (serif fonts are more difficult to engrave, and read, the smaller they get) and what material we are engraving (glass and crystal are more difficult to engrave, and read, with smaller font sizes).
Whenever possible please let our graphic artists assist with font choices and sizes. They will carefully consider the award option you've chosen, the amount of text, and the type of award.
- What fonts are available?
We work with a large variety of serif and sans serif fonts. Generally, we prefer to have our graphic artists make the recommendation on what font to use for your award. They have extensive experience and knowledge about what works best on the award you've chosen, with the amount of text you have, your logo styling, and the type of award you are giving. We will certainly try to meet any special requests, including using customer supplied font.
For some additional information on fonts, please see our Font Choices.
- How much is it to convert my logo?
This depends on your file, and how much time we'll need to spend on converting it to a Vector file type. Generally the cost is somewhere between $50 and $150.00. We can provide you with a quote to do this when you are ready to place your order.
- What if I have changes after the proof is sent?
No problem. This is exactly why we send art proofs out. We want you to be able to check spelling, etc. Your award won't be engraved until you approve your proof.
- Can I see proofs on multiple awards before I decide which one to buy?
Our process is to do art proofs after an order has been placed. This is because our design system is connected to our manufacturing systems.
Engraving Questions
- How much is engraving?
We do not charge extra for engraving your logo or award text on your award or gift item(s).Engraving is included in the price of your item.
If you would like engraving on an additional location on your award or gift, there may be an additional charge for this. We can provide you with a quotation for this option if you'd like.
- What size font can you engrave?
In general we try not to engrave text that is less that 10 pt. We will generally recommend fonts that best suit the award or gift item that you've chosen, the amount of text you'd like engraved, and the type of award you're creating. In most cases we can find a font size and type that will make the most out of your award choice. There will be times, when we will recommend a larger size award to accommodate the amount of text that you require, or we can offer suggestions to shorten the amount of text to accommodate a particular size award.
- Can you engrave my logo?
We engrave company and organization logos on almost every award and gift item. Some items do have a very small engraving space, and are best suited to simple logos. In the few cases where a logo can't be engraved on your item, we can make recommendations about engraving your company or organization name in a special manner to make your award or gift items unique and special.
- Can you engrave product that I own (wine glasses, cheese knives, ornaments, bowls, etc)?
No, we’re sorry, but Awarding You generally does not engrave customer supplied materials. Depending on where you are located, you may have a Things Remembered store ( www.thingsremembered.com) in your local mall. They will often engrave customer supplied materials. Many jewelers will also engrave customer supplied items. You’ll probably need to make some calls to find one that can accommodate you.
- Can you engrave a signature?
Yes, in most cases we can engrave a signature (or many signatures) if you would like to add that to your award or gift item. You will need to ask the person(s) to sign their name using a black Sharpie pen and to engrave it much larger than usual. Then PDF the document and send it to us. Having the signature larger (and thicker) than usually allows us to scale the signature down to the size that can be engraved on your item.
Signatures can be engraved in glass, crystal, on plaques, vases and bowls, and gift items. Very small items may not have enough room to engrave a signature along with your award text. Please consult an Awards Consultant to discuss your item choice and the number of signatures you are looking to add to the piece.
Wording and Layout Questions:
- Do you have standard text for my type of award?
We can absolutely help with the wording of your award. Please check the Awards Ideas and Wording section of our Resources section to find options for your awards.
- Can you help me with wording on my award?
Certainly, email our Awards Consultants for help with your award wording. You can also check our Award Ideas and Wording pages of the Resources Section in our website where we've provided lots of wording options for many commonly created awards.
- How do I layout the text I want to use?
You actually don't need to worry about this at all. Our graphic artists will take your logo and the text you provide, and lay them out on a template of your award or gift choice and create an Art Proof for you to review and approve. With years of experience laying out thousands of awards, our team can provide tremendous insight and assistance in the layout of your project.
- How do I know how much text will fit on my award?
Our graphic artists will review the text and logo for your award or gift, and make recommendations on the font size and layout that best works for your project. In some cases, we may recommend a larger size award to accommodate your layout. In all cases, you will receive an Art Proof to see your logo and text laid out on a Template of your award, so you can review and approve the layout for your order before we engrave your order.
Design and Product Questions:
- Do you create custom awards?
We design and manufacture hundreds of custom awards for clients every year. More information on Custom Awards can be found in our Resource Section.
- Can you add color to my awards?
There are lots of ways to add color to your awards. It depends on the award or gift option you've chosen and the colors you want to add. More information on adding color to your award can be found here.
- Can I get my logo in color on a plaque?
The best way to get your logo in color on plaque is to choose a full color plaque option. We have several choices for this, some with existing color layouts, and some that we can customize just for your application. Examples of full color plaques include: Full Color Globe Plaque, and the Oxnard Full Color Plaque. Ask any of our Awards Consultants for assistance with this.
- What is crystal?
Crystal is made from many of the same raw materials as glass. Lead oxide is added to these raw materials to give the glass extra sparkle.
- How is a plaque made?
There are many types of plaques, but in general, there are are two main components to all of them. A wood, or wood finish board, and a metal top plate. The top plate can be engraved, or color printed with your logo and award text. The plate is then glued to the wood back board.
There are many varieties of wood that can be used for the back boards. They are also available is a wide variety of shapes and sizes. Top plates are available in a wide variety of colors, shapes, and sizes, providing you with many options to create a unique award for your organization.
- What is engraving?
Engraving is a process where material is removed from a product , either by mechanical or laser engraving. For more information on engraving, check our Engraving page in the Resources Section.
- Do you color match Pantone colors?
We are regularly asked to match Pantone colors in a logo on an award. The process for doing this depends on the award chosen. In general there is a Pantone match fee of $50 per color for doing this. This is a one time fee. We can come extremely close to your Pantone colors, but it will not be an exact match because our materials are different that the inks used for Pantone matching in a printing process. More information about our process can be found on our How to Order page.
- Can you recycle awards?
Glass can be recycled. Crystal is not recyclable because it contains some non-recyclable materials. The metal plates on awards are generally aluminum or steel and can be recycled. However, every municipality has different restrictions and guidelines on what can be included in their recycling program so you should check before recycling any award materials.
- What is art glass?
Art glass is glass that has been hand-blown into a variety of artistic shapes.
- Do I have to use the design that's on the award in the website photo?
All our awards start blank and can be personalized with your design and award text. The photos on the website are shown only to provide with ideas on how the award style can be used.
- Do you have a retail showroom?
Awarding You does not have a retail showroom. Our facilities include manufacturing, administrative, sales and support offices. We do offer tours of the facilities for clients with scheduled appointments.
For more information regarding the order process and logo requirements, contact our Awards Consultants for assistance at 800-753-3384.
Instructions for Tax Exempt Orders
If you are a nonprofit or association that has an official tax exemption certificate, issued by your state, please follow these instructions for ensuring that tax isn’t charged on your orders.
For first time tax exempt purchasers (applies to all individuals within any organization), please contact our sales team directly so that we can set you up in our system. Once this process is completed, you will be able to checkout online, tax free!
If you are a returning tax exempt purchaser, but you are still seeing taxes applied from your cart, we have a new process established by our tax compliance partner, Avalara. Please contact our sales team directly so that we can set you up in our system. Once this process is completed, you will be able to checkout online, tax free.
For all tax exempt purchasers, please use only those names and emails that are associated with your approved exemption accounts. Using different emails or logins for your exempt company will not provide you with the exempt credentials.
If you have any questions about purchasing for your exempt company, please contact us for assistance – we are happy to help you with the process. You may also call us directly at 800-753-3384.
Packaging and Shipping
Click here to read our Packaging and Shipping Guide